
Imagination needs reality - ideas need implementation
BioTech
Biocatalysis plays a particularly important role in establishing sustainable economic practices. More and more innovations in white biotechnology are already being used by the chemical, pharmaceutical and food industries, or are being considered for future strategic planning.
We want to have an 'enzymatic' effect for your ideas in the field of biocatalysis and minimise the activation energy necessary for new projects. You can rely on our expertise and experience in the production of enzymes at various scales and our know-how in process development and/or optimisation.
We offer you the best service
Our Biotech technologies
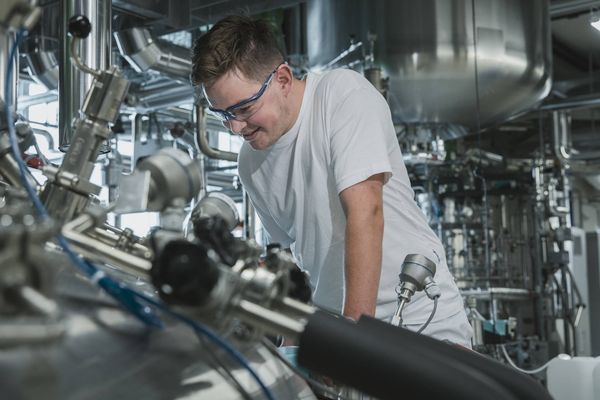
fermentation
Lactosan has three complete fermentation lines, which are controlled by a process control system and can be fully sterilised.
Production
4 media tanks
5000l, 1000l fermentation pre-stage
2 x 15000l fermentation main stage
Pilot plant
16l fermentation pre-stage
700l, 300l, 150l fermentation main stage

separation
Fermentation is followed by a concentration step using a separator.
Production
10000 l/h separation
Pilot plant
100 l/h separation

homogenisation
In the homogenisation step, the biomass is broken down and the enzymes are released.
Production
2 x 1000 l/1000 bar homogenisation
Pilot plant
120 l/1000 bar homogenisation

precipitation
In order to increase the purity of the enzyme product or to improve subsequent filtration steps, it is possible to integrate a precipitation step into the production process.

concentration
In the enzyme production process, ultrafiltration and diafiltration systems are used to concentrate the product and for buffer exchange respectively.
Production
400 l/min crossflow ultra/diafiltration
Pilot-Plant
60 l/min crossflow ultra/diafiltration

DNA-depletion
DNA depletion is another optional step in the enzyme production process to increase the purity of the product.

filtration techniques
The filtration system allows removal of the production organism or components thereof in the product, at the customer's request.

freeze-drying
The aim of freeze-drying is to obtain a dried, readily water-soluble product that retains the properties of the original product after the addition of water.
Production
1000 l/batch freeze-drying
Pilot-Plant
60 l/batch freeze-drying

grinding
After drying, further processing takes place on the relevant powder line. The product flakes dried by lyophilisation are crushed in mills.

mixing
After the drying and milling process, the powder is processed on the relevant powder line and the final product is mixed according to specification.

packaging
After processing on the relevant powder line, the dried powder is filled according to customer's requirements.
Filling
300g to 30kg bag
